Lean Manufacturing (Production)
Introduction
In today’s industrial scenarios, organisations are competing against each other by manufacturing or providing better products or services. There are various products or services like mobiles, automobiles, airlines, hospitals etc. are available and to choose the best one is solemnly depend on the customer’s perspective. On this process, they procure a ton of activities which doesn’t add value either to producers and consumers. Eventually, it leads to inefficiency in workflow and bad quality impacts.
By implementing Lean methodology, we can reduce or eliminate such activity which doesn’t add value in a process. It goes beyond eliminating waste and works to create a culture of continuous improvement. Thus it leads to an increase in productivity, reduces costs, highly enhances quality products or services and gains customer satisfaction. During initial phases, it was largely applied in manufacturing sectors and as time passes by it found its application in various non – manufacturing sectors (healthcare, airlines, banks, etc.) also.
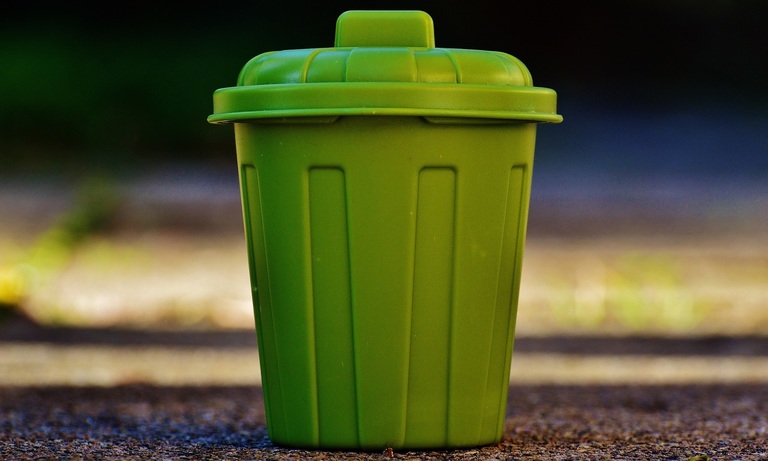
What is Lean?
Lean is a methodology used for eliminating waste and for continuous improvement of a process. A Lean process is faster, more efficient, more economical and delivers quality satisfactorily. It removes an activity which doesn’t add value to the process such as defects, overproduction, extra – processing, etc. This approach can be implemented in both the manufacturing and service industries.
The major focus of lean is to prioritize customer’s requirement and thus gain customer’s value. To achieve customer’s value, it works to eliminate waste from the areas like defects in a process, overproduction, waiting time, non-utilized talent, unnecessary transportation, excess inventory, motion and extra-processing. Lean is all about delivering finest quality with reduced cost. Some of the common tools used in Lean Manufacturing are Value Stream Mapping (VSM), Kaizen (Continuous Improvement), Kanban, Jidoka and so forth.
There were many evolution phases about the origin of lean manufacturing. Many writings were published by elite personalities about the origins of Lean. The concept of Lean was continuously stimulated with the changing period and needs of an organisation. Let’s discuss some of the major phases about its origin.
Ford’s Assembly Line – It was introduced on December 1913 by Henry Ford. The main objective was to increase the production of “Model T” automobile and to reduce the cost. Here, the resources – personnel, machine, and equipment were ordered in such a manner that there was always a continuous flow of production. Hence it reduced the time to build a car from Twelve hours to Two hours and Thirty minutes. However, there was a limitation that it lacked variety and was applied to only one specification.
Toyota Production System (TPS) – Sakichi Toyoda (Founder of Toyota Group) was the initial contributors towards the TPS. He introduced the “Jidoka” concept and defined as “automation with human touch”. After the World War II, Japan was shattered and it was impossible for automobile company like Toyota to compete with the foreign automakers. Then Eiji Toyoda, Taiichi Ohno and other executives visited to the United States to study the Henry Ford’s system. They inspired from the Ford’s Assembly Line and came up with a way to keep the assembly line idea going, as well as providing the variety that customers were looking for – leads to an invention of “Just in Time Production” (Known as Toyota Production System). It aims to reduce the cost of production, enhance the quality of products and meet the customer’s expectations.
This overall concept was popularly introduced to the World in 1990 as “Lean” through the book titled “The Machine that Changed the World “by Daniel Roos, Daniel T. Jones, and James P. Womack.
Waste is any activity that doesn’t add value to a process or a service but it consumes time and other resources. There are eight areas from where wastes are produce and Lean manufacturing focus on eliminating it.
To remember the eight wastes, we can use the acronym “DOWNTIME.“
- Defects – It leads to rework, scrap and eventually loss of time & resources by involving in wasteful activities. More defects mean more waste. Similarly, fewer defects mean less waste.
- Overproduction – Producing more products or services that are needed. Thus overproduction leads to trash.
- Waiting – Idle time or delay created by waiting for the next process step. For e.g. during a process hours labours are waiting for raw material and other resources.
- Non Utilized Talent – When an employee has the potential to do tasks but management fails to utilize it. It means failing to utilize employees talent, skills and knowledge.
- Transportation – Moving products or materials unnecessarily from one place to another. Thus adding no value to the products or services.
- Inventory – Excessive products or materials are store than required. For e.g. equipment or materials are kept idle without usage.
- Motion – Extra steps taken by personnel which don’t add value to a process. And it could be either machine or parts which are doing unnecessary movements.
- Extra Processing – Doing additional processing i.e. beyond customer’s requirement and don’t add value to product or services. It costs extra money and resources.
There are certain principles in Lean methodology which helps to eliminate waste and ensures continuous improvement in an organization.
Let us discuss in brief about it.
- Define Value – The first and foremost priority is to understand the customer’s value. What is the value? Value is something that the customer is willing to pay for. So define value from a customer’s perspective. Without them we are nothing and moreover, they defined us. Therefore it is necessary to understand the process that adds value to a customer.
- Identify and create value stream – The second lean principle is to identify and create value stream. Here, we will identify the activities which are adding value to a process and eliminate which are useless to a process. It can be categorized into value added and non-value added activities.
- Create Flow – To create a continuous movement of personnel, materials and equipment in a process. Thus it ensures continuous flow system in producing products or services without interruptions or delays for next steps.
- Establish Pull – To avoid excess inventory, we should establish a pull in a process. Here, we will be producing products that required and deliver on time which adds value to a customer. It means scheduling a process.
- Strive for perfection (Continuous improvement) – To strive for perfection, there should be always continuous improvement in a process. It means to provide quality products or services consistently. To ensure it, we should follow the first four principles systematically.
- 5S (Workplace Organization) – It is a key component to organize workplace. By implementing it, we could reduce waste, increase safety and make efficient flow in a process.The 5S are –
- Sort – To make arrangement of the items which are needed in a work place. And to remove the unnecessary items.
- Straighten – To prepare a specific location where we can keep resources and so it will easier to maintain it.
- Shine – To maintain cleanliness in workplace by cleaning equipment, storage and so forth. By doing so, we can reduce waste and improve efficiency.
- Standardize – There should be some sort of standards in a workplace to conduct 5s. So that everyone would involve in a process.
- Sustain – To be consistent in fulfilling the previous steps and thus maintain the same flow from beginning till the end of a process.
- Value Stream Mapping (VSM) – It is a fundamental tool in lean manufacturing which helps to reduce waste and increase efficiency in a process. It is a pictorial tool that represents the process scenarios like flow of a product and development, identify wastes and highlight flaws which affects the process. By using VSM, we can have better insights of a process and gain different perspectives about the process flow. It displays all the important steps of a process which are required from initial to final phases of a products or services. Thus brings clarity in a process.
- Jidoka – Sakichi Toyoda introduced this concept and popularly known as “automation with human touch”. It is a key concept in Lean manufacturing. It is all about stopping a process when a problem arises. Then to evaluate the cause for it and come up with corrective plan instantly. Thus prevents to produce defective products or provide bad quality services.It consists of the following phases.
- Detect a problem
- Stop a process
- Review & fix the problem
- Come up with corrective plan
- Just in Time (JIT) Manufacturing – Taiichi Ohno introduced this concept. It is a methodology to establish pull in a process. It refers to a required production of goods or services in specific time and to deliver efficiently. Thus it eliminates wastes from over – production and excess inventory. Some of the benefits are increase in production, cost reduction, employee’s empowerment and hence leads to good quality impacts.
- KANBAN – It was developed by Taiichi Ohno. KANBAN plays a prominent role for effective implementation of JIT. It is a visual board which gives the information about the ongoing process and schedule the process. It ensures that the process is producing goods to customers as required. Basically, it signals the operators when to run the process. It requires continuous monitoring of a process.
- KAIZEN – The term ‘KAIZEN’ means Continuous Improvement.
And this Improvement could be in process, products, services, personnel, etc. It includes everyone in a process starting from ground level workers to top level executives in a continuous improvement environment. The main purpose to implement KAIZEN is to improve productivity, eliminate non-value added activities (waste) and make a continuous flow in a workplace. It works on “PDCA Cycle”.
- Plan – Plan for improvement by setting goals and gather possible information about a process.
- Do – Execute the plan; involve everyone and it leads to appropriate results.
- Check – Examine the results and we would come to know how effective our plan.
- Act – Take action based on above results i.e. to implement it or not.
- Total productive maintenance (TPM) – In order to have a good production system in a company, machines and equipments should be properly maintained. TPM is a major tool in lean environment – helps to avoid breakdown, fewer defects and no accidents. OEE (Overall Equipment Effectiveness) is important measure in TPM. It is a metric used for TPM productivity. OEE is measured by three criteria i.e. availability (no breakdowns), performances and quality. An OEE score of 100% is a perfect production system.
Attend our Training Program, to know – “How can we achieve Quality Excellence in an Organisation?” We conduct various training programs – Statistical Training and Minitab Software Training. Some of the Statistical training certified courses are Predictive Analytics Masterclass, Essential Statistics For Business Analytics, SPC Masterclass, DOE Masterclass, etc. (Basic to Advanced Level). Some of the Minitab software training certified courses are Minitab Essentials, Statistical Tools for Pharmaceuticals, Statistical Quality Analysis & Factorial Designs, etc. (Basic to Advanced Level).
We also provide wide-ranging solutions for Enterprise Quality Management to achieve Organisational Excellence.